
The Ro-Lab Difference
APPLICATION
REQUIREMENTS
-
Abrasion Resistance
-
Chemical Resistance
-
Oil, Water or Both
-
Cut and Tear
-
Dynamics
INITIAL
DESIGN
-
3D Printing and Soft Tooling
-
Prototypes
-
D.F.M. (Designed for Manufacturability)
-
Material Choice
-
FEA and Closed Solutions
CUSTOM
FORMULATIONS
-
Polyurethane:
- Polyether
- Polyester
-Specialty -
Rubber:
-Natural
-Nitrile
-SBR
-Silicone -
Plastics
MOLDING
PROCESSES
-
Hot Cast and Ambient Cast Polyurethane
-
Injection Molding for Plastic, Rubber and Urethane
-
Compression Rubber Molding
-
Transfer Molding
-
RIM (Polyurethane)
EXPERTISE
-
Precision Molding to RMA-1 Standards
-
Rubber- and Urethane-to-Metal Bonding
-
Insert Molding
-
Molding of Large, Thick Parts and Intricate Parts
-
Formulation Expertise
EQUIPMENT
-
Over 100 Presses, Up to 80" wide
-
Capacities up to 2500 tons
-
Rubber Platens Up to 20 feet long
-
Oven Capacities to 2800 Cubic Feet (20' x 12' x 12')
EPSCO Territory:
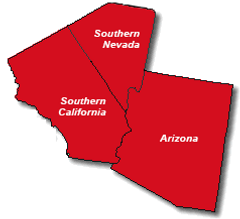
What We Can Do:
-
Review your application
-
Provide technical assistance and product advice
-
Show samples based on possible product approaches
-
Retrieve further application details required for a quote
-
Visit your facility, no charge
We are your local
DYNATECT
technical sales and
customer service contact!
Ro-Lab's Custom Molded Rubber & Urethane Products are based on 100 + years ofdiverse molding, casting, extrusion and mandrel made molding experience
Ro-lab's roots date back to The American Rubber Co. Inc. founded in 1906 in San Francisco. The American Rubber Co. was a pioneer in manufacturing fire hoses that were sold across the United States. Their fire hoses laid the ground work and entrepreneurial spirit to expand product offerings into agriculture, industrial, mining and military markets. Ro-Lab Rubber Co. started as a testing and consulting business to the tire industry and quickly moved into custom mixing and molding of rubber products. American Rubber and Ro-lab Rubber merged in 1978 into a company eminently qualified to serve the diverse molding, casting, extrusion and mandrel made needs of their many customers.
The Ro-Lab facility, located in Tracy, California, now occupies 65,000 square feet of manufacturing space and is capable of compounding and manufacturing a complete range of rubber and polyurethane products from standard compounds to custom designed formulas. Their customized approach to design and manufacturing allows us to have total production control from their customers’ specifications to final finishing, ensuring products of consistently high quality. Ro-lab's specialized equipment, polymer chemistry knowledge and extensive production expertise are aimed at delivering the tightest tolerances, most rigorous quality control and highest standards in aesthetic appeal.
Click Below for more Dynatect Brands:
![]() |
---|
![]() |
![]() |
![]() |
![]() |
![]() |